November 2020 | 1663 words | 6-minute read
Tata Power has an installed generation capacity of about 12.7 gigawatts (GW) across thermal, hydro, solar, and wind sectors. “Power generation is an asset-intensive business,” says Hasit Kaji, chief digital and information officer, Tata Power, “which is why it is important to keep our operations and maintenance (O&M) expenses at an optimum level. This coupled with the growth the company is planning for renewables has been the focus over the past few years and will significantly increase in the years to come”.
Tata Power embarked on a digital industrial journey across its thermal and renewable power plants and kicked off multiple initiatives. Among these is the Reliability Centred Maintenance (RCM) initiative for ensuring high availability of its plants and reduction of O&M costs. Similarly, the Autonomous Power Plant initiative is aimed at improving the operational parameters to cut down fuel spends. At its renewable power sites, the company is leveraging digital to manage remote generation assets through the Central Control Room for Renewable Assets (CCRA) initiative.
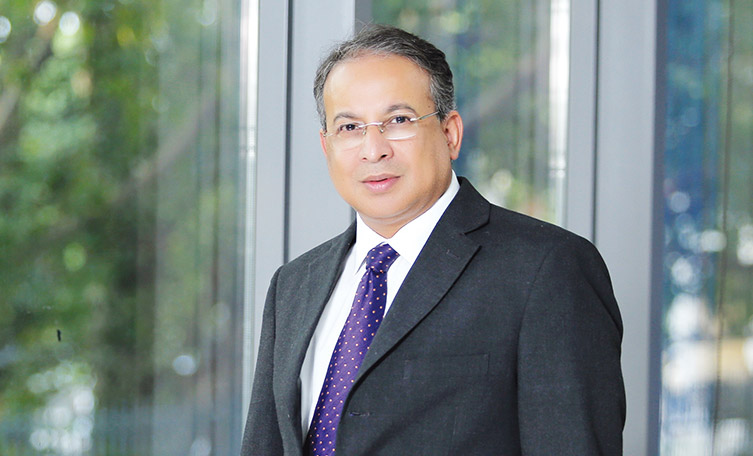
"The power sector is going through a huge transformation due to the integration of electrical technology with IT. This is facilitating utilities like us to improve productivity and provide real-time data and information. Consumers too play an active role in usage of electricity. This along with decentralised energy is changing the way energy is being produced and consumed.
"To continue serving our consumers we are investing resources in development and adoption of new and safe technologies. All our upcoming projects – grid-scale and distributed renewable plants, distribution networks and serviceled businesses – are packed with smart digital processes and data analytics. We have been expanding our operational footprint and setting new benchmarks for operational efficiencies using technology solutions and redefining paradigms.”
—Mr Praveer Sinha, MD & CEO, Tata Power
Reliability-centred maintenance
Plant maintenance is based on a mix of reactive, preventive, and predictive techniques. Preventive maintenance, traditionally applied in power plants based on manufacturer recommendations, are overly vague and err on the side of excessive maintenance.
To improve asset reliability and usher in a new paradigm of maintenance, the RCM initiative was launched in October 2016. The goal was to make O&M digital — data and analytics driven. Existing systems were integrated to capture all plant maintenance and operational data for a holistic analysis of asset failure and to formulate accurate predictive asset strategies. The focus was on minimising failure rates, optimising maintenance cost, increasing asset life and uptime. Operator rounds at the site were digitised through use of field devices which were integrated with the RCM to improve maintenance effectiveness.
What really helped the initiative achieve momentum was involving the O&M teams at all levels since they would be the end users of this initiative. ‘One Tata Power way of working’ was inculcated right from design to implementation. “But what we needed the most was a shift in perception that data can help everyone do their jobs better,” says Vijay Namjoshi, chief – generation, Tata Power.
While implementing the RCM, foundation elements like equipment codification, classification, failure mode effect analysis (FMEA), and data quality were taken up across all divisions. With a well-defined hierarchy conforming with international guidelines (ISO 14224:1999), assets were codified and classified based on criticality across all divisions.
As data was central to the analysis and maintenance strategy, data quality in the SAP system was ensured. FMEA is one of the most important steps in the RCM implementation. It involves creating an exhaustive list of failure modes of equipment, causes, possible actions to prevent failure or reduce its impact in the future. As no published asset failure catalogue existed for the power utility sector, Tata Power created its own asset failure catalogue. The core implementation team, constituting cross-domain experts and OEM representatives, carried out the FMEA.
Workshops were conducted across divisions on how to formulate maintenance strategy based on data analytics. IIT (Indian Institute of Technology) professors in reliability engineering were brought in to train the team on data analytics. Aakar, an NGO based in Ahmedabad, Gujarat, helped the plant workforce adopt this new way of maintenance through skits and ground-level activities.
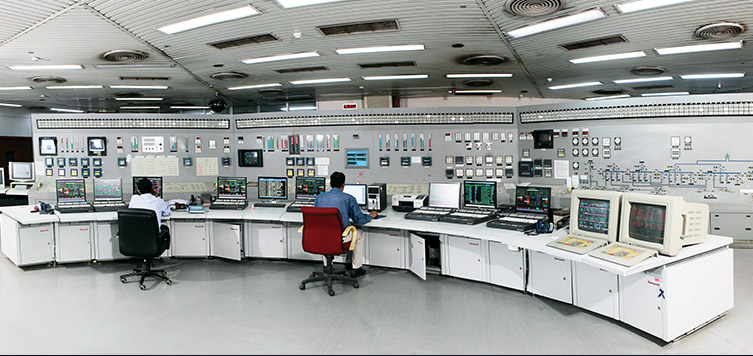
Following its successful implementation in December 2019, the solution is being used by all divisions for day-to-day maintenance activities such as asset health management, maintenance strategy optimisation, and operator routes. Advanced analytics is providing plant leaders granular views into assets and helping them take more informed decisions. This initiative has enabled Tata Power define optimum maintenance strategy for critical assets, resulting in improved mean time between failures (MTBF) and mean time to repair (MTTR).
Tata Power is the first power company in the country to adopt data analytics for asset performance management in the O&M value chain.
Autonomous power plant
While the RCM is helping improve maintenance parameters, other digital interventions are improving operational efficiency. The most notable is the Autonomous Power Plant (APP) initiative. This is a first-of-its kind in the Indian power sector for improving the operational regime and the plant heat rate.
“As part of the Autonomous Power Plant programme, a ‘digital twin’ was piloted for the boiler at the Maithon Power Plant. Following successful outcomes from the pilot, the digital twin implementation is being scaled up,” says Mr Kaji.
Heat rate is the function of many variables; an operator manually adjusts the operating parameters during transient condition like load throw-off, coal quality changes, etc, to achieve the best possible levels. However, due to the sheer number of variables, it is not possible to manually maintain parameters at optimum values to achieve the best heat rate consistently.
Based on the operations data collected over 24 months, the digital twin uses artificial intelligence (AI) and machine learning (ML) based models to assess these operating variables. It provides real-time advisory to the operator to run the plant in the most optimal manner. This has resulted in improvement in the unit heat rate. “After validation of the AI/ML models in part load and full load regime, the models will go-live and then model advisory will be used for control room operator guidance,” says Mr Namjoshi.
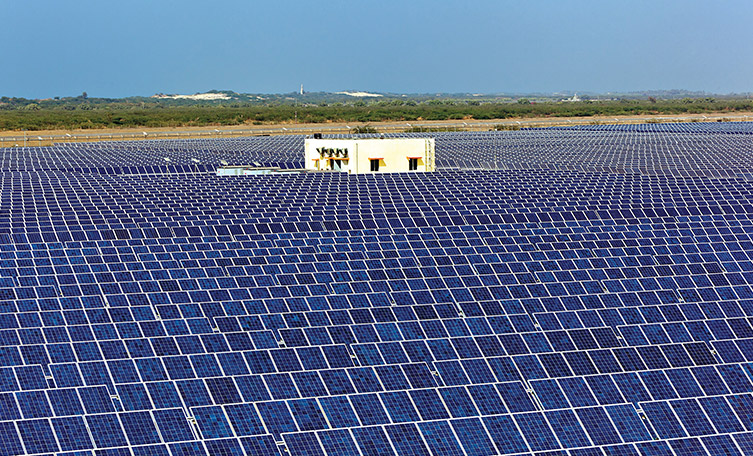
A reduction of 1 kcal/kWh of heat rate in a thermal power plant can result in annualised savings of around ~Rs 30 lakh. “This year, we are looking at a reduction of 10 kcal/kWh of heat rate, and over the next 2-3 years we are looking at a reduction of 20-30 kcal/kWh,” says Mr Kaji. Thermal power contributes to the majority of Tata Power’s overall generating capacity. While it is sweating its thermal power assets, Tata Power is also growing its renewable sites by ~6 times (reaching ~15GW) by 2025.
Central control room for renewable assets
To enable real-time monitoring, diagnostic and analysis of assets of all renewable energy plants, Tata Power set up the CCRA in 2019 in Trombay, Mumbai. Tata Power has about 3GW of renewable energy generation capacity. Of this, CCRA has a view on 1GW with a plan for extending it to the balance capacity of ~2GW by this financial year end, with a provision to further extend it to future capacity additions.
Asset monitoring and data analysis enables the company to forecast how much power it can generate the following day by accounting for factors such as weather conditions, asset conditions, etc. Accurate forecasting is crucial to the generation business as power companies have to comply with their declared capacity. While 15 percent variance is allowed, anything outside of that is considered a deviation and attracts a penalty. Apart from assisting the forecasting team to minimise these penalties, CCRA also serves as a single source of truth for all renewable energy assets across sites.
“Earlier, the performance of the renewable energy sites was getting monitored at the plant level because we didn’t have data at the turbine, solar panel or inverter level,” says Ashwinikumar Patil, CEO of Tata Power Renewable Energy Ltd. “So, we started collecting data at the granular level by connecting the sites to a central control room. Now that we are getting this data, we have a better sense of where things are going wrong and are building algorithms that send automated alerts to the site team that can then take proactive actions to correct the problem,” he adds
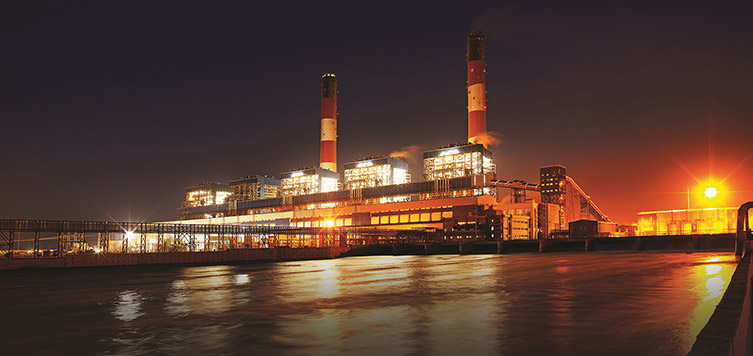
The first phase of CCRA was operational in July 2019 for about 1GW of renewable capacity across 18 locations, including for 15 wind energy sites and three solar energy sites. These assets were connected to CCRA using an IoT platform for the first phase. For the second phase of implementation, Tata Power has developed an open source in-house platform that would implement advanced analytics for performance modelling, predictive maintenance, and early detection of problems.
To create an in-house talent pool, Tata Power launched the Data Analytics and Insights Academy. A select group of employees was chosen to undergo a three-month programme on descriptive analytics under the mentorship of academic and industry experts. The first batch completed training in March 2020, and they have already started applying the learnings across multiple initiatives. The academy continues to train batches and is integral to building Tata Power’s competency in advanced data analytics.
Early benefits of CCRA are already evident. Tata Power Renewables saves Rs 1.6 crore per year which on per unit basis is an industry benchmark. The proactive identification of low-performing inverters across all the renewables sites has enabled Tata Power to take corrective actions with the OEM. This has improved conversion efficiency by 2–3 percent and generation as well.
Even as these initiatives are helping improve asset performance, Tata Power is already planning ahead and exploring the possibility of leveraging these platforms to provide service to external customers. “This can be a good business opportunity,” says Mr Kaji, adding, “All we need is to connect the plants, collect the data and run the models. Our algorithms are proven and ready to run.”
—Abhishek Mande-Bhot