July 2020 | 2010 words | 8-minute read
As the manufacturing sector adapts to the Covid-19 world, TV Narendran, MD & CEO, Tata Steel, comments on the impact of the pandemic on industry, and the way forward.
What impact have the pandemic and the subsequent lockdowns around the world had on the manufacturing sector?
The manufacturing sector, like all other sectors, has been significantly impacted by the pandemic.
Firstly, manufacturing companies have fairly complex supply chains, with inputs coming from multiple places and multiple vendors. So even in normal times, managing the supply chain is challenging. During the pandemic, managing the supply chain was a huge challenge due to the multiple restrictions in different countries and different parts of India.
Secondly, there is an impact on the customer front. A steel company, for instance, caters to various sectors of the economy, like automotive, construction and appliances among others. If any sector that consumes steel is impacted, sales are affected and that has an impact on production.
Finally, manufacturing companies typically depend on permanent labour and contract labour, and the movement of both was affected due to the lockdown.
For Tata Steel specifically, there were various degrees of impact across the world. None of the geographies had as complete a lockdown as India. We were operating at about 60 to 70 percent production levels in the UK and the Netherlands. In Southeast Asia, operations were reasonably normal because Singapore and Thailand initially seemed to have handled their response to the pandemic quite well, though Singapore later had a complete lockdown because of a recurrence of cases.
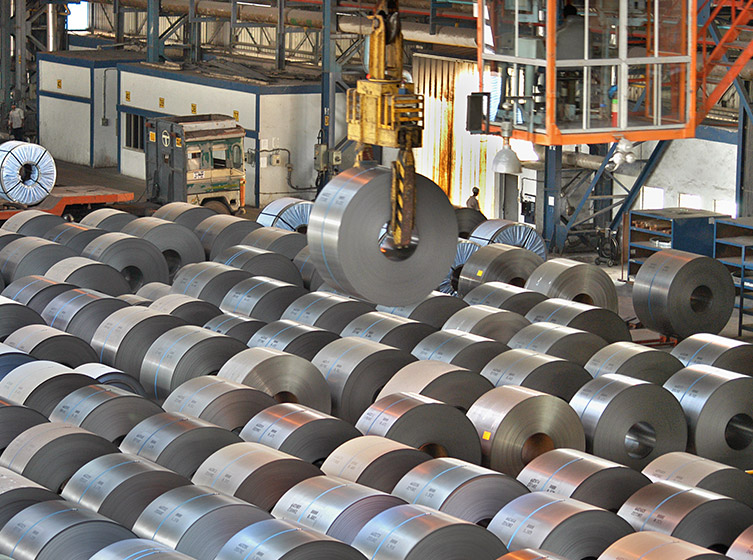
As lockdowns are lifted and restrictions eased across the world, what kind of challenges do you anticipate going forward?
I do expect a challenging year or two ahead. This pandemic is not going away any time soon. There may be a recurrence or future partial lockdowns. One challenge is that we will have a fairly disrupted inbound and outbound supply chains for the next two years. So, companies have to be agile and resilient.
Another challenge is that there will be a fair amount of macroeconomic stress, which will impact households and consumption. Customers will take time to come back to normal levels of activity, hence demand will take some time to come back. Again, if there are job losses, consumption will be further impacted. It might take a few quarters or a few years depending on which geography you are in.
There is also the question of how much of an appetite different governments have to spend their way out of trouble. There have been a lot of announcements, but we will need to see how that flows into the real economy and brings back confidence, which is required to bring back consumption. The government can create demand by spending on infrastructure, which will help with a quicker recovery. If we wait for the sentiments to come back on consumption, it may be a longer haul.
Specifically with regards to Tata Steel, how have business plans for the year — either actioned or in process — been impacted?
We are a capital-intensive industry and have a significant amount of capex planned for every year. So firstly, because demand is uncertain and having high leverage is a challenge, we have decided to focus on cash, on deleveraging, or at least ensuring that leverage does not increase.
We will continue to spend on sustenance, safety, environmental and health-related capex. But anything to do with growth will be deferred until the right time — anything to do with taking out costs or improving the value of our products will be prioritised over growth. We have also focussed on taking out both fixed costs and variable costs significantly. On the revenue side we have decided to focus on a much higher share for export, even as we wait for domestic markets to recover.
How has Tata Steel used the lockdown period to strategise for the future and to build in competencies to adapt to the new normal?
Tata Steel has a number of strengths but agility hasn’t traditionally been its strongest characteristic because we are a process-driven organisation, which believes in continuous improvement and running a very stable operation.
Over the last year or so, however, we had been working a lot on agility, and this crisis was an opportunity to test our ability to be agile. I was quite happy with the response — the way teams worked together to respond to the disruption of supply chains, kept the plant running despite the disruptions, looked for alternate markets when the home markets were disrupted, looked at exports, changed the product mix as appropriate, and so forth. The question now is, how can we preserve this agility even after the crisis?
From a strategising point of view, we are determined to build more resilience into our supply chains, in terms of mitigating risk and over-dependence on some geographies, countries or vendors. We have always had fairly strong risk management practices, but we are reviewing these very closely because the velocity of the coronavirus has caught us by surprise. However, I must say that because of our footprint across geographies, we had started some preparation well before the lockdown, and were better prepared than many of our peers in India.
Moreover, for about three years, we have been spending significantly on technology and a year ago, we moved to the Cloud. This couldn’t have been more timely, because we very easily shifted to the work-from-home environment, with no disruption to business and operations. So, the investments that we made in technology have been more than remunerative.
We have also used this crisis to conduct a number of experiments in operations, which we can’t do with the plant running at full capacity. As a consequence, when things come back to normal we will be able to take out far more costs, because we will work with different operating regimens.
How has the focus on markets changed on account of changes in demand and supply across geographies and industries?
We have struggled because the auto industry, which buys around 20 percent of the steel we make, has not recovered yet and may take more time. We need to find alternate markets, which look for high-quality steel.
In terms of geographies, in Europe we are currently operating at 60 to 70 percent and we will have to continue at that level because the continent might take a bit longer to bounce back to normal. In Southeast Asia, Thailand has not seen a major impact, while Singapore has, but it is likely to be back to normal this month as the lockdown is being lifted. The India business is our biggest and the most profitable, so we’re aiming to get the business back to normal here as soon as we can.
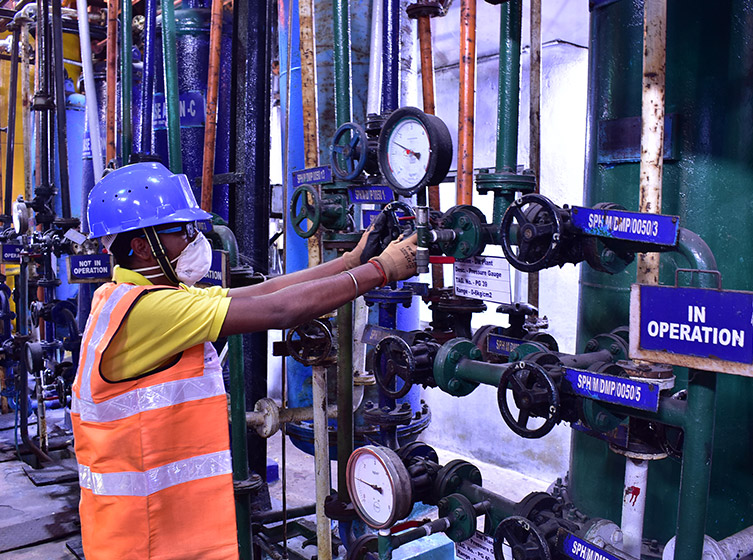
As many plants move towards operating at full capacity, safety is an important discussion. How is Tata Steel going about reconfiguring workspaces and developing new protocols?
Safety has always been a very important part of the way we work, given that at the Tata group our employees are one of the most important stakeholders. We are very particular about not putting any employee at risk. So step one is to ensure that the minimum number of people required come to the workplace, whether that’s a factory or the office.
In the operating plants, we have staggered shifts and have provided employees with all necessary personal protective equipment, including masks. Workspaces and buses that ferry employees to the plants are frequently sanitised, and social distancing is observed everywhere, including at the gates, where we follow strict protocols for checking everyone who enters.
We are using a lot of technology to track how plants are operating. In Angul (Odisha), we used drones to check if social distancing is being followed in remote parts of the plant. We use analytics from RFID (radio-frequency identification) cards on contract workers to track if there is a clustering of people at any plant at any site, and we use video analytics to check if people are wearing masks.
Until mid-April, Jamshedpur was the only major Indian city without a single Covid-19 case, so we’ve been reasonably successful in our collective efforts — the doctors, security people and employees, including our contract workers and regular workers.
What are the opportunities or learnings that have emerged during this pandemic and lockdown, in your opinion?
Any crisis is an opportunity for us to look in the mirror. It tells us what we’re good at and what weaknesses we need to iron out; it gives us a lot of data on the organisation, and how the leadership and the people cope with a situation. There’s a wealth of information that emerges, which hopefully helps us run things differently.
One of the learnings is that productivity can go to very different levels — whether it’s productivity of people, space or time — if we leverage technology that we’ve had all along. For instance, it’s strange that before March, I’d never used Microsoft Teams, even though I’ve had it on my iPad. This whole crisis has helped us better leverage the money that we’ve spent so far on technology. Now the question I ask HR is, at least for office staff, “Do you really need attendance?” In the last three months we’ve moved towards a culture of measuring people by the quality of work they do and the output they deliver. It doesn’t matter what location you work out of, as long as you deliver what you’re supposed to. There’s an opportunity to build flexibility into HR practices so that we can leverage talent better.
We’ve also had an opportunity to look at different revenue streams. We already had a Services and Solutions business; now we’re building ready-to-use houses, which can be used as isolation centres, and can also build hospitals quickly, along with many other such facilities. So, we’re looking at how we can monetise a lot of capability that we have to provide technical services and go beyond our traditional revenue streams, because traditional revenue streams will be vulnerable over the next few years to the fluctuations in the physical world.
How do you envision the journey back to normalcy, if at all returning to the old normal is possible?
First and foremost, we have to accept the fact that this virus is going to be around for the next few years. So the question is, how do we ensure that we don’t put our employees at risk, even as we go about coming back to — if not normal — close to normal? A lot of protocols and practices will change, and I’m confident that people will adapt to it. I’ve already seen it when I went to the plant in Jamshedpur, when I visited Mumbai or when I’m at the airport.
There are many good things that will come out of the crisis. At the individual level, hygiene will improve. From a large number of people in India falling ill or dying because they don’t wash their hands enough, to washing our hands every time we walk past a washbasin — the change is huge.
At the institutional level, I hope it will encourage more expenditure on the health infrastructure. We have always underspent on health, and I hope this builds more consciousness around it.
From a manufacturing point of view, if there are products that you supply, which were essential during this crisis, then you look at expanding that part of the business. For instance, steel is pretty much used in everything, including building a hospital, constructing hospital beds, and making ventilators.
People will seek to de-risk their supply chains, and thus more Indian consumers in the B2B space will want to source locally, which is an opportunity for us. The pandemic will accelerate some of the China de-risking work that has been going on for the last two years. And that also creates opportunities to grow manufacturing in India, if you can address some of the challenges. The manufacturing segment will have to recalibrate, but it’s also a great opportunity for Indian manufacturing to emerge stronger.
—Anuradha Anupkumar