May 2025 | 1772 words | 7-minute read
Picture this: You are sitting in a state-of-the-art training facility. As you put on a virtual reality (VR) headset, you are transported to a construction site, complete with cranes, concrete batching plants, loaders and earthmoving machinery. You can interact with the equipment, understand the controls, and, if there is a mechanical failure or an emergency, you know exactly how to remedy the situation.
This is not an escapist gaming experience, but a highly realistic way of learning. It is also one of the many technologies that Tata group companies are employing to improve safety standards on sites.
Employee welfare and safety have been a key cornerstone for the group since inception in 1868. For N Chandrasekaran, Chairman, Tata Sons, the focus on strengthening processes and practices to achieve zero harm — to people, the environment and assets — remains a top priority. “We are embarking on a huge expansion phase, where every company is adding capacity, be it electronics, manufacturing, semiconductors, batteries or telecom,” he said, at the 2024 Tata Business Excellence Convention. “There are nine new plants we are building at the same time — all of which will start operations within the next two years. We cannot achieve manufacturing and business excellence if safety is not addressed adequately.”
Strategic building blocks
Across the group, there is a common thread running through zero harm workplace initiatives — the thrust on employing Industry 4.0 technology and digital tools, like automation, artificial intelligence (AI), internet of things (IoT), robotics, augmented reality (AR), data analytics and cloud computing to make operations more intelligent, connected and, above all, safe.
At Tata Steel, safety initiatives are driven by the company’s commitment to achieve zero harm across operations by 2030 and it is consistently incorporating mechanisms to assess safety risks and initiating preventive measures. “Industrial safety is a two-way commitment — an organisation’s commitment to develop effective strategies and practices whose success depends on the stakeholders’ commitment to adherence, caution and vigilance,” emphasises Jayanta Banerjee, Chief Information Officer, Tata Steel. “Industrial safety involves preventing hazards resulting either from people’s actions, their interaction with the work environment and/or equipment condition.”
Tata Steel uses a Safety Performance Index to assess each division using a set of lead and lag performance indicators. While lead indicators are proactive measures that help predict and prevent potential issues, lag indicators measure and provide insights into past safety performance and outcomes. “We analyse these indicators to identify trends and areas of improvement, ensuring that we learn from the past,” says Mr Banerjee.
One of the company’s many personnel safety initiatives is the installation of special wireless sensors throughout the plants and creation of geo-fenced zones that are categorised as hazardous/non-hazardous, based on their operational state. Tata Steel has also issued RFID-based Suraksha cards to ensure workforce safety and security within the premises. The sensors transmit real-time locations of Suraksha cardholders, ensuring comprehensive situational awareness. All this feeds into Tata Steel’s AI-enabled Connected Workforce platform.
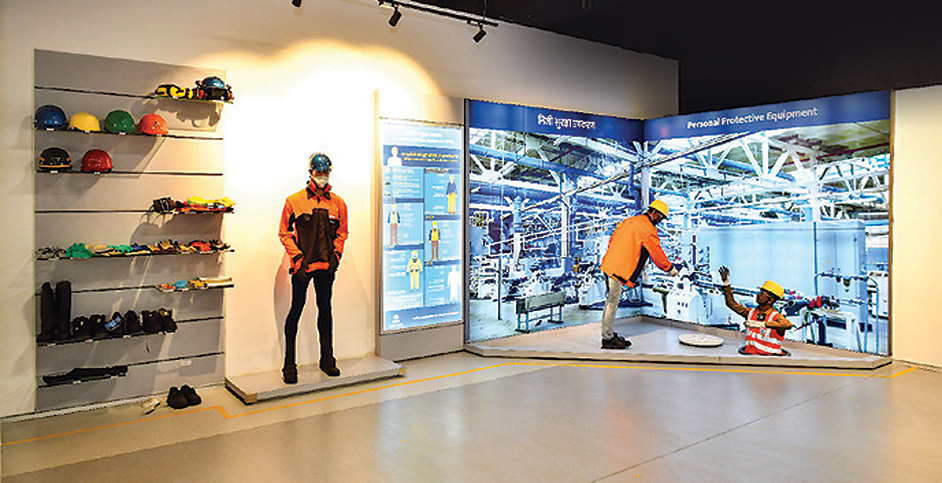
“More than 40,000 sensors have been deployed and 1.5 lakh Suraksha cards have been distributed,” says Mr Banerjee. “The cards, along with image analytics, are used for detecting unsafe conditions, like PPE [personal protection equipment] violation, restricting unauthorised personnel and pre-empting unauthorised entry in hazardous areas. The in-built SOS button can be used for immediate rescue.”
Another initiative is the Integrated Remote Operations Centre (iROC) for centralised remote monitoring and supervision through real-time tracking and enforcement of safety measures.
Tata Steel’s operations also present unique safety risks, like run-over incidents involving heavy earthmoving machinery, underground mining hazards and maintenance activities done by outsourced partners. Some controls introduced to address these risks include driver fatigue monitoring systems, roof stability enhancements in underground mines and smart fencing solutions.
Metrics matter
Elevating safety standards requires more than just tracking numbers. Metrics like Total Recordable Injury Rate (TRIR) and Near Miss Reporting Rate guide decision-making, but the real challenge lies in transforming data into meaningful insights and proactive safety measures.
“Managing environment, health and safety (EHS) across 200 projects, spanning multiple geographies and a workforce of over 60,000, is quite challenging,” says Yogesh Srivastava, Head - EHS, Tata Projects. “The key to making a real impact lies in knowing where to focus efforts.” Manual data collection was slow, error-prone, and paper-intensive, creating bottlenecks instead of driving improvements. So, the company developed TQDigi’lytics, an in-house digital platform for monitoring and recording EHS activities. This was a shift from passive record keeping to proactive risk management.
Next, the company put in place a metric to analyse the data and glean insights — Safety Risk Index (SRI®), built around 14 leading indicators. This enabled real-time risk quantification, identification of high-risk areas, and implementation of strategic risk reduction plans.
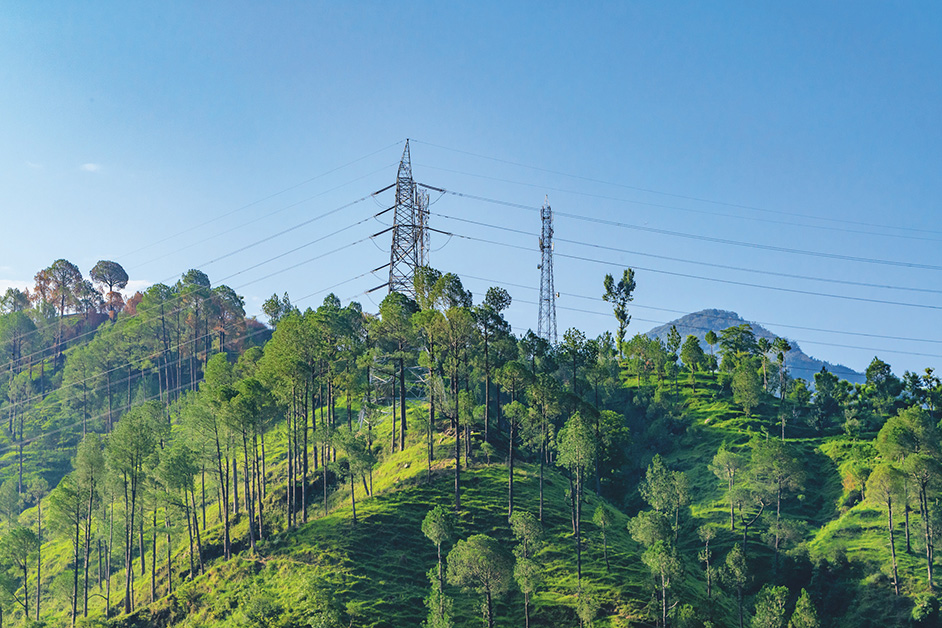
One particularly valuable insight came from analysing near misses. Potential Severe Events (PSEs) — critical near misses and observations — were identified as an untapped goldmine for learnings. The company established a structured system, where every month, HSE professionals and operations leaders analysed TQDigi’lytics data to pinpoint PSEs, design mitigation strategies, and implement corrective actions across all sites. This continuous improvement cycle has been instrumental in preventing repeat incidents.
Additionally, drones now monitor hazardous and hard-to-reach areas, replacing risky manual inspections. AI-powered cameras and IoT-enabled vehicles provide real-time safety analytics, enhancing risk identification. “Moreover, the innovative use of technology for internal applications, such as employing drones in stringing activities to replace high-risk, labour-intensive methods, and using laser projections for hazard zone marking, stood out in improving safety outcomes,” Mr Srivastava adds. The company has deployed these interventions on projects such as the Noida International Airport, Mumbai Trans Harbour Link and the Pune Metro Rail.
Beyond physical safety, Tata Projects has also focused on worker well-being. The company is working on introducing wearable sensors to track body temperature, heart rate, and hydration levels in real time, triggering alerts to prevent heat-related injuries. Encouraged by the pilot’s success, the company is planning to implement this across multiple sites.
The impact of their various initiatives has been significant. Lost Time Injury Frequency Rate (LTIFR), which measures incidents that lead to an employee spending time away from work, dropped by 90%, from 1.126 in FY23 to 0.122 in FY24, and the Safety Risk Index declined by 13 points. The company has received global recognition, with multiple projects winning at the 2023 and 2024 International Safety Awards by the British Safety Council and a Silver Award at the RoSPA Fleet Safety Awards 2024.
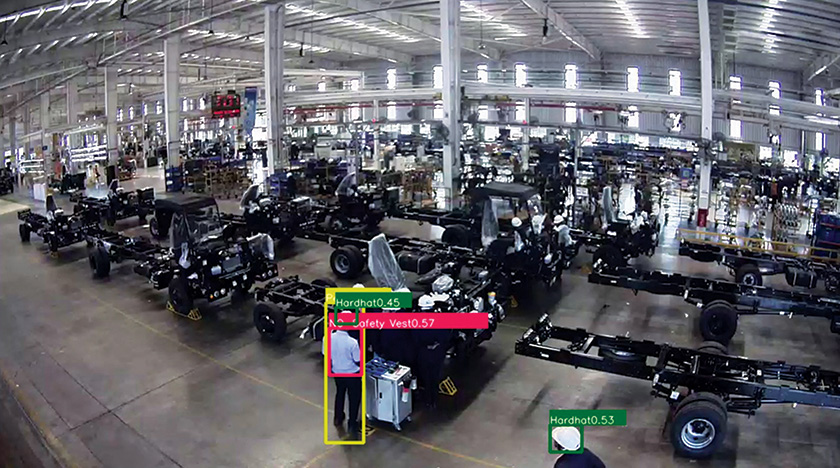
Digital safeguards
Tata Motors too has moved towards a predictive and preventive safety culture, deploying AI, IoT, video analytics, and connected workforce solutions to detect hazards and mitigate risks in fleet operations and lone working environments, to drive safer work practices. “Reducing the risk exposure of humans engaged in high-hazard activities has been the core of our design principles for implementing automation and digital monitoring solutions,” says Vishal Badshah, Vice President and Head – Operations, Tata Motors Commercial Vehicles. For instance, the company now has manless entry and exit gates at plants, IoT sensors to monitor conditions in hazardous areas, biometric authorisation to ensure only authorised personnel operate forklifts, and has deployed robots and cobots (collaborative robots) for activities with high exposure to safety and other risks in the manufacturing environment.
The digital interventions have reduced injuries, improved equipment reliability, thereby reducing breakdowns and associated risks, and enabled a faster response to unsafe situations. By the end of Q3 FY25, Tata Motors’ total recordable case frequency rate had reduced by 27% compared to FY24.
Overcoming barriers
A common but formidable challenge that all companies face is effective adoption among the workforce, notes Mr Badshah. “Transitioning to digital safety solutions requires sustained structured training and behavioural reinforcement,” he says. Mr Srivastava of Tata Projects agrees, “Traditional work practices have made the adoption of digital tools, drones, AI, and IoT slow. We now require extensive awareness programmes.”
Towards this end, Tata Steel has established Safety Leadership Development Centres in Jamshedpur and Kalinganagar, where employees and contract workers are trained using AR/VR to improve their risk perception of critical hazards without having to step on the shopfloor.
In 2024, Tata Power set up a first-of-its-kind VR and 4D experience safety training centre for its transmission force. Located in Mumbai, the centre provides immersive simulations for the company’s engineers and linesmen where they live through scenarios so as to learn to anticipate risks and hone their instincts.
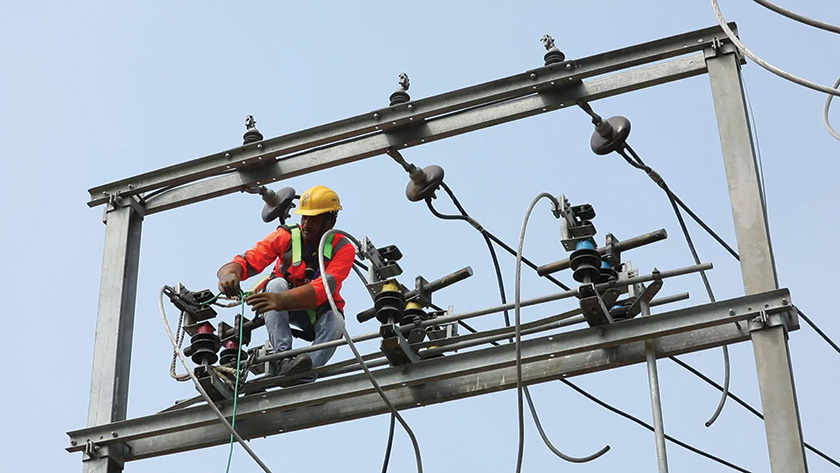
Mr Banerjee believes technology can only go so far and some human supervision is essential. The challenge then is to find the right balance for a collaboration between humans and machines. “We call this human-in-the-loop decision-making,” says Mr Banerjee. “An example is our Safety Leadership Development Centre, where we monitor safety non-compliances. It’s possible the camera incorrectly identifies a non-violation as a violation due to the rules applied to the specific use case — this is a false positive. To prevent false positives from entering the system, human intervention is necessary.”
Other challenges faced include ensuring new technologies comply with industry regulations, safety standards and security, as handling vast real-time data from multiple sites requires data protection, encryption and cloud-based solutions.
The human factor
While AI can generate effective solutions through pattern recognition and statistical inference from large datasets, it doesn’t ‘think’ in the same way people do. Therefore, there is no replacement for original thinking, and solutions often come from human ingenuity. For instance, a Tata Power engineer designed and developed a drone in-house for boiler roof sheet inspection to address the problem of loose sheets atop 16 boilers in Haldia, West Bengal, a region prone to cyclones. Earlier, inspecting the steel sheet required 108ft high scaffolding, which was both high risk and costly. The team now uses the drone to identify critical locational defects through a high-resolution camera and plan for rectifications well before a cyclone.
Smart safety
The roadmap to zero harm looks different for different Tata companies. While Tata Power plans to integrate psychological safety — an approach that reinforces learning proactively from successes — into its next initiative, Tata Motors is developing AI-powered tools to extract deep insights from textual data to identify specific risk patterns and digital lock out/tag out systems to reduce risks during human-machine interactions. Tata Projects, on the other hand, is overhauling its current ecosystem and aims to launch Hubble, its next-gen centralised safety management system that employs enhanced analytics, seamless AI integration and geo-fencing, later this year.
Regarding the debate on whether zero harm is possible, it turns out that achieving zero harm is as much a journey as it is a destination.
—Anju Maskeri